IoT機器やセンシング技術の導入により、生産・保守のフェーズにおいて部材/仕掛品や設備のデータを自動的に収集することができるようになりました。
しかし、多くのお客様から、IoTデータの活用についてよくご相談を受けます。センサーで収集したIoTデータはデータベースに保存して蓄積されているものの、「製造条件のトレーサビリティ」や「歩留り向上のための分析」以外にこれといった活用がされておらず、せっかくのビッグデータが十分に使われていないようです。
一方、現実世界(リアルワールド)をコンピュータの仮想空間(バーチャルワールド)に再現するデジタルツインが注目を集めています。デジタルツインの構築には、現実世界のデータが必要です。センサーやカメラなどのIoT機器によって集められたデータは、まさにこの現実世界のデータであり、IoTデータとデジタルツインを掛け合わせた「IoT×デジタルツイン」は、製造業の生産現場に大きな変革をもたらすテクノロジーになり得ると期待されています。
デジタルツインとは?
デジタルツインは現実空間のコピーをコンピュータの仮想空間にバーチャルに再現する技術です。現実空間とそっくりな双子を仮想空間に作り出すことから、デジタルツインと呼ばれています。現実空間の事象をセンサーやカメラで捕捉してデータ化し、コンピュータに送信します。コンピュータはセンサーやカメラから受信したデータをコンピュータで処理を行い、現実空間のコピーを仮想空間に作り出します。このコンピュータに作り出された現実世界のコピーこそがデジタルツインです。そして、その仮想空間を人間が使用することで、現実空間ではできない体験や予測をしたりすることで、現実空間でのプロセス改善やアウトプット向上を目指すことができます。
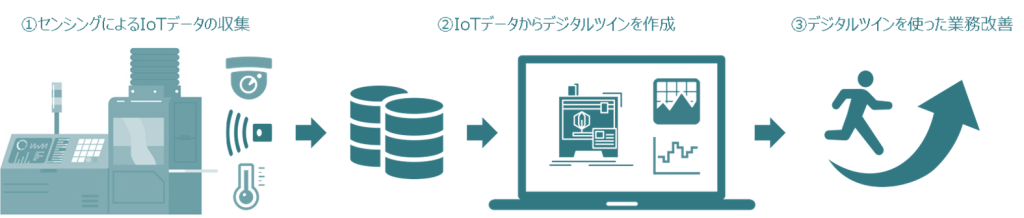
デジタルツインで何が出来る?
デジタルツインの目的は「コンピュータ上の仮想空間に再現したデジタルツインを活用して業務改善に繋げる」ことです。本記事では、製造業の工場(生産ライン)を想定して、デジタルツインを活用することで実現可能な業務改善の例についてご紹介します。
■設備の遠隔コントロール/自動化
コンピュータ上に再現したバーチャルな生産設備を使って、工場に担当員を配置することなく、オフィスの執務室から生産設備を稼動させることが出来るようになります。
生産設備の稼動状態をコンピュータ上に表示することで遠隔監視が可能であり、さらにその稼動状態を見ながら、コンピュータを操作して生産設備を開始/停止することができます。(必要なIT技術:5G)
■設備のバーチャルトレーニング
AR・VR技術を活用すれば、生産設備の3Dイメージをコンピュータ上に再現することができます。生産設備の3Dイメージは、バーチャルに操作することが可能であり、設備の操作方法やメンテナンス手順を繰り返し実施して、担当員の習熟度を上げるトレーニング環境として使用できます。(必要なIT技術:AR・VR)
■設備の異常検知
生産設備をセンシングしてコンピュータに送信し、生産設備の稼動状態(電圧/電流値、圧力値、ストローク量など)をモニタリングすることができます。
この生産設備の稼動データが蓄積されてくると、そのデータから生産設備の故障の発生を予知することが出来ます。(必要なIT技術:シミュレーション/機械学習)
■生産品質のコントロール
例えば射出成形では、射出成形機の状態が生産品の品質に影響します。この品質への影響を最小化するために、生産設備の設定値や外部環境のデータを取得し、現在および将来の生産品の品質を予測することもできます。(必要なIT技術:シミュレーション/機械学習)
バーチャルセンサー
先にご紹介したデジタルツインの活用事例の中で、「設備の異常検知」や「生産品質のコントロール」では、シミュレーションや機械学習の技術を活用します。このシミュレーションや機械学習を活用して異常検知や品質予測をする処理を「バーチャルセンサー」と呼びます。バーチャルセンサーとは、その名前の通り現物が存在する物理的なセンサーではなく、入力データを与え、シミュレーション/機械学習を使って入力値を知りたい値に変換して出力する仮想的なセンサーです。すなわち、バーチャルセンサーによって、物理センサーが検知した値から実際に知りたい値に変換することができます。
では、バーチャルセンサーはどのような場合に役立つのでしょうか?
物理センサーはどこにでも好きなところに取り付けられるわけではありません。例えば、センサーを取り付ける十分なスペースがなかったり、センサーが動作不可能な高温環境では、物理センサーによるセンシングは不可能です。そのような場合、別の場所にセンサーを取り付けて、そこのデータを取得し、そのデータからバーチャルセンサーを使って、実際に知りたい(けれど、センサーを取り付けられない箇所の)データに変換することが可能になります。

それでは、ミニ四駆とラズパイを使って「IoT×デジタルツイン」と「バーチャルセンサー」を表現してみます。
図解「IoT×デジタルツイン」と「バーチャルセンサー」
■ミニ四駆
タミヤ社が製造・発売している四輪駆動の自動車模型です。小型電動機を搭載し、単3型乾電池2本を動力源として走行します。工場の生産設備をミニ四駆に置き換えて表現しています。
■ラズパイ(Raspberry Pi)
ARMプロセッサを搭載したシングルボードコンピュータであり、イギリスのRaspberry Pi 財団によって開発されました。
日本では通常「ラズパイ」と呼ばれています。
工場の生産設備に搭載または付属している制御システムをラズパイに置き換えて表現しています。
* ミニ四駆は株式会社タミヤの登録商標(日本第2168392号ほか)です。
* Raspberry Pi はRaspberry Pi財団の登録商標です。
目標は「ミニ四駆を安定走行させること」
ミニ四駆を長時間、安定走行させることを、この事例の目標とします。
この事例は、「IoT×デジタルツイン」と「バーチャルセンサー」を簡単に説明するため、ミニ四駆が安定走行するために必要な要素を「モーター」に限定し、モーターが安定動作するための要素を「コイル温度」に集約していますが、実際にはそのようなことはありませんので、ご注意ください。
【ミニ四駆を安定走行させるためのシナリオ】
1、ミニ四駆を安定走行させるためには、モーターの内部状態を正常に保つ必要があります。
2、モーターの内部状態を正常に保つためには、モーターの内部状態を知る必要があります。
そして、モーターの内部状態はモーターのコイル温度から予測可能です。
3、モーター内部にセンサーを付けられないため、モーター内部のコイル温度は検知出来ませんが、
モーターの筐体温度はセンシング可能です。
4、モーターのコイル温度は、シミュレーション技術と機械学習を使うことで、モーターの筐体温度から計算することができます。
5、モーターのコイル温度が閾値を超えたら、バッテリー電圧を操作してモーターを止めることで、
モーターのコイル温度を下げることができます。
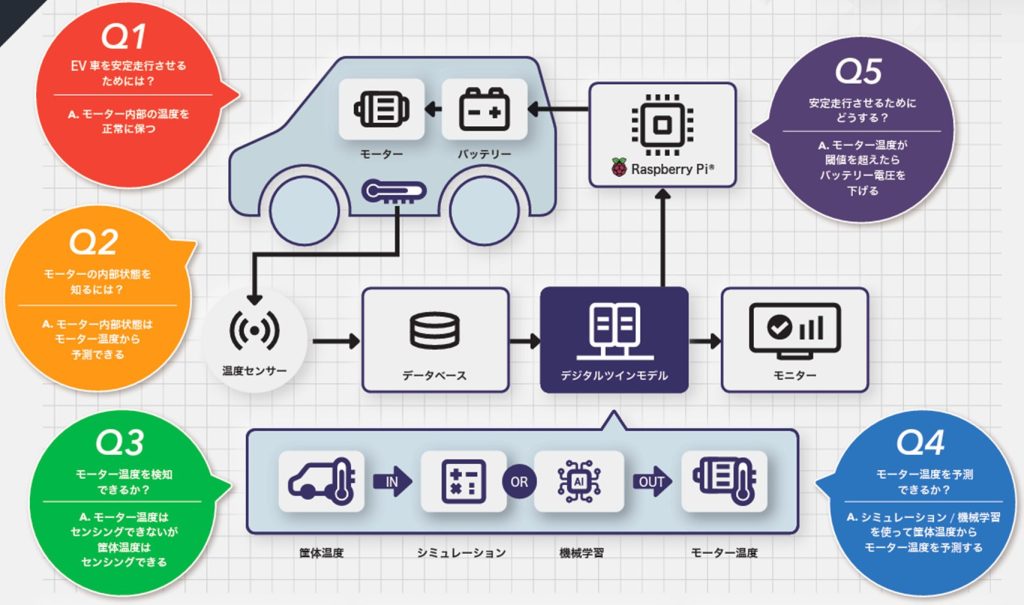
このシナリオでは、ミニ四駆を安定走行させるために、モーター内部のコイル温度をモーター外部の筐体温度からシミュレーション技術と機械学習を使って計算しており、この計算回路(図3のデジタルツインモデル)がバーチャルセンサーにあたります。
このバーチャルセンサーは、電気回路と熱回路の連成によって実現されており、図4のようにモデリングすることができます。このバーチャルセンサーは、モーターの筐体温度をモーターの内部温度に変換するだけの単純なモデルですが、「時系列データへの対応」「入出力の多重化」「モデルの複数化」などの、より複雑なモデルにすることもできます。
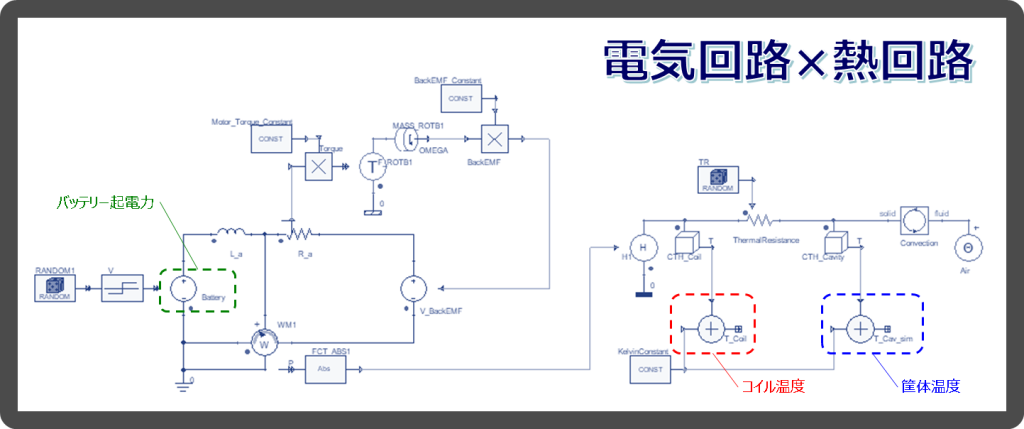
デジタルツインは現実空間のコピーをコンピュータの仮想空間にバーチャルに再現する技術です。そのため、この事例では、現実空間であるミニ四駆の走行状態をコンピュータ上に表示する必要があり(表示しないと、現実世界で起きていることを、人が認知できない)、その表示例をご紹介します。
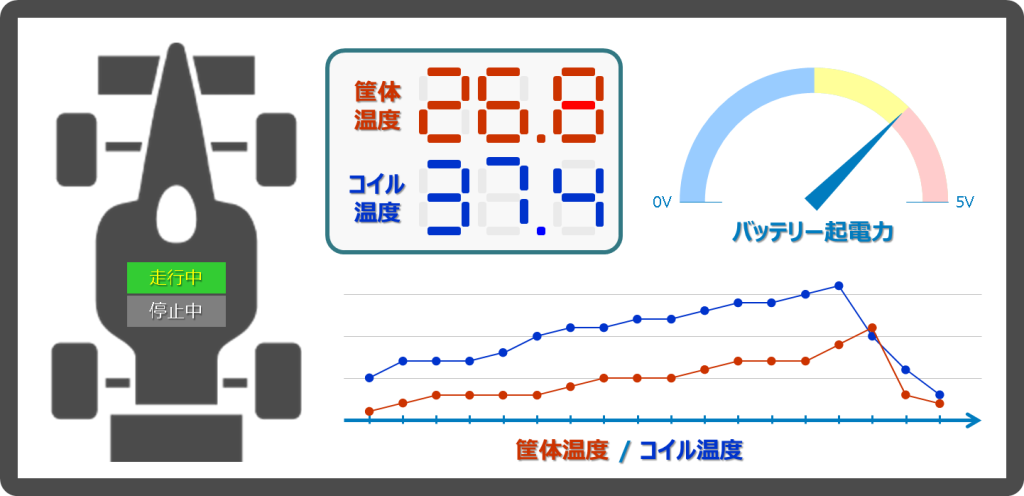
バーチャルセンサーが適用可能な事例
生産工程について次のような課題を抱えていませんか?
工場の生産工程は、定期的な生産設備のメンテナンスや生産品の検査が欠かせません。また、生産設備の停止時間や歩留りの悪化は生産効率の低下に直結します。
「IoT×デジタルツイン」と「バーチャルセンサー」によって、生産効率の向上に繋がる次のような改善活動を実施することができます。
■適用例1:生産品の品質の可視化
例えば射出成形は、原料や金型および成形機の状態によって成形時の状態は時々刻々と変化し、その変化は生産品の形状に影響します。また、射出成形は数十秒~数分間隔で連続成形しますが、その際、成形機から得られる様々なデータからこれから成形する生産品の形状を予測します。
■適用例2:装置の故障予知
例えばボールねじ装置では、連続動作することによって、ボルト/ナットの緩みや軸の摩耗/温度上昇が発生することがあり、それらは装置の故障に繋がります。そのため、速度やトルクなどの制御機器から得られるデータや、振動や移動速度などのセンサーから得られるデータから、装置の異常発生を検知/予測します。
■適用例3:設備のメンテナンスの最適化
例えば3Dプリンタでは、造形物の品質を保つために造形時の酸素量を緻密にコントロールする必要があります。しかし、造形時の酸素の流入を防止するシール材は、装置の使用とともに徐々に劣化するため、定期的なメンテナンスが必要です。造形時の酸素量の周期変化を検知することで、3Dプリンタのメンテナンス時期を予測します。
まとめ
本記事では、IoTデータの活用事例として「IoT×デジタルツイン」をご紹介しました。また、様々な目的・用途に応用可能なデジタルツインの中でも、バーチャルセンサーによる設備の予知保全や生産品質のコントロールについて、ミニ四駆とラズパイの事例を使ってご説明しました。
本記事でご紹介した「IoT×デジタルツイン」の実現には、バーチャルセンサーの実現が欠かせません。お客様が抱える課題をバーチャルセンサーとして表現できない(モデリングできない)場合、「IoT×デジタルツイン」は実現できません。そのため、バーチャルセンサーのモデリングの実現が最初のハードルとなります。
バーチャルセンサーを活用したデジタルツインの構築手順
本記事でご紹介した「IoT×デジタルツイン」と「バーチャルセンサー」の構築に際し、JSOLは次の 3 Stepでの推進を推奨します。
Step1:バーチャルセンサーのモデリング[実現可否の検証]
お客様が抱えている課題がバーチャルセンサーで解決可能でなければなりません。センシング可能な値から課題解決に直結する値に変換する処理を、シミュレーションや機械学習を使って実現可能かどうかを検証します。
Step2:IoTデータとバーチャルセンサーの接続[プロトタイプ]
お客様環境に「IoT×デジタルツイン」を構築します。ただし、クローズ環境(インターネット等、外部環境に接続されていない環境)を使用します。お客様の生産ラインに設置したIoT機器から上がってくるデータをバーチャルセンサーに入力し、当初の目的/目標が達成されることを確認します。
Step3:IoT×デジタルツインの実現[プロジェクト]
Step2で構築した「IoT×デジタルツイン」をオープン環境(OA-LANや工場LANに接続されている環境)に移行し、イレギュラーケースへの対応を織り込みます。デジタルツインの結果を生産ラインの制御にフィードバックさせる場合、事前の十分なテストを実施してから開始します。
パイロットユーザー募集中
現在、JSOLでは本記事でご紹介した「IoT×デジタルツイン」の心臓部にあたる「バーチャルセンサー」について、ベンチマークテストを実施させて頂けるお客様を募集しております。
本記事にご興味のあるお客様は、下部の「パイロットユーザー応募はコチラから」ボタンをクリックしてご応募下さい。
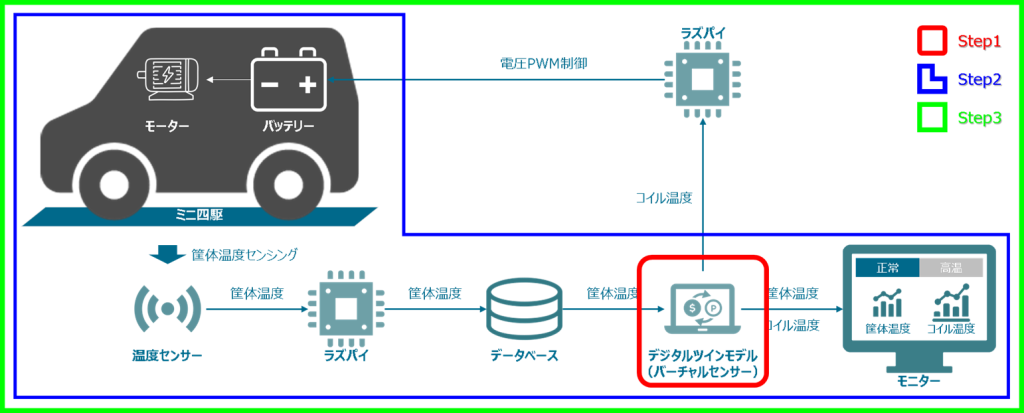
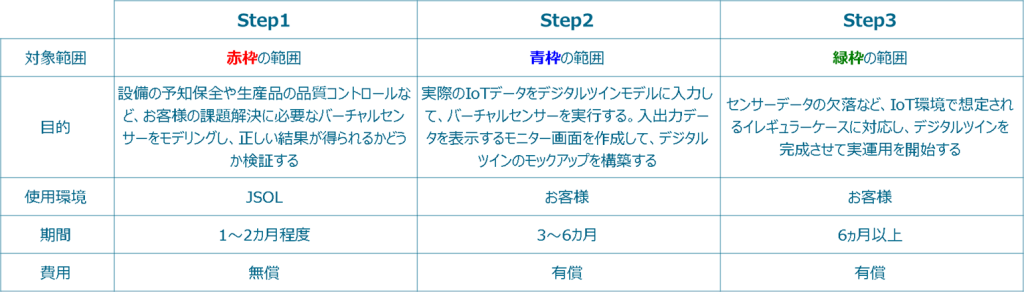
【補足事項】
・ベンチマークテストは、24年1~3月頃の開始で、最大3社程度を予定しています。そのため、応募頂けるお客様が多数の場合、お客様の課題内容によって、JSOLにて選定させて頂く場合がございますので、ご了承ください。
・ベンチマークテストの開始前に、機密保持契約を締結させて頂きます。また、機密保持契約書に従って、お客様よりデータ提供を頂く必要がございますので、ご了承ください。
・ベンチマークテストの実施にあたっては、事前にスケジュールを作成しますので、そのスケジュールを遵守頂くようお願いします
・ベンチマークテストの結果が良好の場合、後続の「Step2 PoC(Proof Of Concept)」のご提案をさせて頂きますので、あらかじめご了承ください。